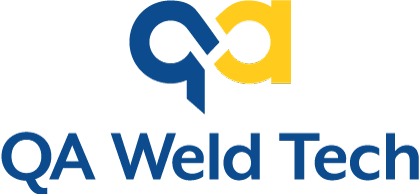
We are delighted to launch our new branding and website. The new and fresh image forms a key part of our strategic plans to diversify into new markets, including:
- Petrochemical
- Valves and pumps
- Rail
- Marine
- Nuclear
- Power generation
Three years ago, we put in place a strategy that has seen us invest heavily in facilities and personnel, developing our management team and systems to produce a more rounded company with a skill set that transfers readily across many industrial sectors.
We believe that our new, sleek and quality image very much represents the business that we are today, appealing to both our new and existing target markets.
As QA Weld Tech enters into these new sectors, we have ambitious plans to transfer our solid pedigree and reputation for delivering complex welding and fabrication services.
Want to know more, contact our Business Development Director, Andrew Dean at ADean@qaweldtech.com.
View our new brochure